在焦炉煤气制LNG 工业化应用
上海华西化工科技有限公司
(联系人:纪志愿13817279096 余浩13761112739;)
摘要:本文介绍了一种工艺流程短、能耗低、投资小的焦炉煤气甲烷化制LNG 工业化工艺 技术,并与其它甲烷化工艺技术进行对比。该技术全流程均为华西公司开发、具有自主产权、 在国内实际应用的技术。目前,采用该技术的曲靖市麒麟气体能源有限公司的LNG 工厂已 顺利投产。
关键词:焦炉煤气;甲烷化反应;工业化
1、前言
国内独立焦化企业每年副产焦炉煤气约900 亿m3 。有关焦炉煤气的综合利 用一直焦化企业非常重视的问题。以前焦炉煤气主要作为市场工业原料甲醇、合成氨的原料,以及回炉加热自用、工业用燃料、发电等等。最近几年投产的以及 新建的焦化装置,由于国内甲醇、合成氨产能过剩,投资收益大幅度下降,甚至 出现亏损,因此寻找新的焦炉煤气的利用途径成为了焦化企业面临的难题。随着 近些年来天然气价格的节节攀高,焦炉煤气制天然气(管输天然气、压缩天然气CNG、液化天然气LNG)备受关注,该技术能量利用效率高,工艺流程简单,市场前景看好,正逐渐成为焦炉煤气综合利用的具有较强竞争力的新领域之一。
近年来,国内多家设计和研究单位加大了焦炉煤气甲烷化制天然气技术的工 业化、商业化,目前已有多地处于规划、拟建或在建阶段,也有工厂投产运行。
2、焦炉煤气甲烷化制LNG 工业化应用及工艺路线
上海华西化工科技有限公司(以下简称上海华西)开发并总承包的日处理量 为20.4 万Nm3 焦炉煤气和3.6 万Nm3 高炉煤气的低温甲烷化制LNG 工业化装置,2012 年下半年在曲靖市麒麟气体能源有限公司成功投运。装置从焦炉煤气预处理、脱硫、甲烷化到干燥的全流程均采用由上海华西自主开发的新型技术。其中液化部分采用国内MRC 混合制冷技术,甲烷化技术采用上海华西公司开发的等温甲烷化技术。
该项目焦炉煤气制LNG 工艺流程示意图如图1 所示:
如图 1 所示,装置主要分为压缩、预处理、脱硫、甲烷化、干燥、液化等几个单元。 1)压缩单元
压力为~10KPa.G焦炉煤气和高炉煤气经压缩机加压到0.2~0.6MPa.G 后送入预处理单元,除去萘、焦油、苯等杂质后返回压缩机加压至1.6~3.0MPa.G 后送 至后续脱硫单元。
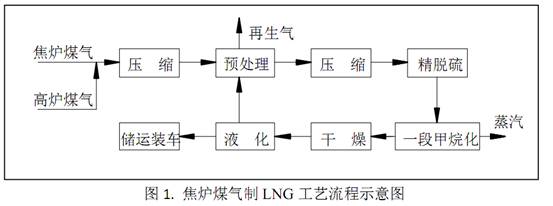
2)预处理单元
装置采用的预处理工艺流程简短,催化剂寿命长、性能高。有效脱除了焦炉煤气中的苯、萘、氨、焦油等常见复杂杂质,保护后续脱硫、甲烷化催化剂和冷箱。
3)精脱硫单元装置采用的两段”脱硫工艺,解决了中温有机硫催化剂氧中毒、积碳、脱硫剂副反应及硫化物回收等问题,脱硫后总S<0.5ppm。
4)甲烷化单元装置采用的新型一段等温床甲烷化反应器使流程大为简化,投资、能耗大幅降低,出口二氧化碳的含量至50ppm 以下,采用低中温抗结碳镍基甲烷化催化剂使反应效率大幅提高。装置核心部位甲烷化部分实际运行表明,等温甲烷化技术采用低温280°C下反应,避免了催化剂高温失活,省去了补加水蒸气抑制催化剂积炭,有利于反应平衡向产物方向移动,大大提高了甲烷化产率,实际运行中,在

中H2含量在约5%)时,一氧化碳转化率≥99.95%、二氧 化碳转化率≥99.9% 以上。整个装置工艺流程短,成本低,节能效果显著,有望解决焦炉气排放造成的环境污染和资源浪费间题,为高碳能源低碳化利用奠定了基础。
5)干燥单元
甲烷化后得到的气体不能满足液化单元的技术要求,在液化前要进行净化处理,即除去原料气中的水分和杂质,如H2O、Hg 等,以免它们在低温下冻结而堵塞、腐蚀设备和管道。干燥单元可采用变温吸附的脱水工艺,干燥后气体中水的含量< lppm(常压露点低于-70°C)。干燥后的气体进入脱汞塔脱汞,脱汞塔为装有载硫活性炭的填料塔,脱汞塔出口汞含量小于0.01μg/m3,出脱汞塔的气体经过过滤器脱除夹带的活性炭粉尘后进入液化工段。
6)液化单元
装置采用国内混合制冷剂(MRC)制冷技术,净化后的甲烷化气进入冷箱内的各段换热器被返流的低温介质冷却,在一定温度下以汽液混合物进入气液分离器,气相部分富(H2/N2体)进入LNG 过冷器过冷LNG 后去主换热器复热送出冷箱至净化部分做再生气,液相部分节流后进入塔中部进行精馏,塔釜获得LNG 经过冷器过冷后送至常压LNG 贮罐中储存;塔 部抽出驰放气回主换热器复热后送出冷箱至净化部分做再生气。
上海华西为内蒙建元焦化设计的日处理量为40.8 万Nm3 焦炉煤气制LNG 装置安装已结束,预计于2013 年8 月开车。
另据报道,国内首套焦炉煤气制天然气项目是太工天成2007 年在山西河津实施的焦炉气综合利用新工艺示范工程,该项目中没有甲烷化工艺,采用前端组
成净化、膜分离、低温液化等技术生产LNG 和H ,项目于2009 年建成,但由于各种原因,该工程一直未正常开工。另外,乌海、菏泽、重庆等地焦炉煤气制天然气项目正在规划、拟建或在建,这些项目中均有甲烷化工艺,但甲烷化技术主要由国外技术商提供工艺技术和催化剂。
3. 等温甲烷化技术与国外甲烷化技术的比较
甲烷化反应是指气体CO 和CO2 在催化剂作用下,与氢气发生反应,生成甲烷的强放热化学反应。通常工业生成中的甲烷化反应有两种:
一种是用于合成氨及制氢装置中,在催化剂作用下 合成气中少量碳氧化物 (CO+CO2 <0.7%)与氢反应生成水和惰性的甲烷,以削除碳氧化物对后续工序催化剂的影响。自1902 年发明了用于催化甲烷化反应的镍基催化剂以来,化肥生产中用于甲烷化的催化剂和工艺绝大多数围绕这类催化剂进行研究。
另一种是人工合成天然气工艺中的甲烷化,其原料气中的碳氧化物(CO+CO2)浓度较高。以煤制合成气为原料的合成天然气的甲烷化研究始于20世纪40 年代,在经历了 世纪70 年代的石油危机后,人们又开始重视以煤为原料生产合成天然气的研究工作,从而使合成天然气的研究进入高速发展时期。
3.1上海华西甲烷化技术 甲烷化反应是强放热反应,其反应方程为:

每1%C反应生成甲烷,气体的绝热温升约为83℃,1%的CO2反应生成甲烷,气体的绝热温升约为70℃。
对此,上海华西专门开发了特殊的等温列管式甲烷化反应器。甲烷化催化剂装在管中,水在壳程。发生反应时,通过高压水的沸腾排热,控制甲烷化反应的温升。由于等温列管反应器可使甲烷化在较低温度下运行,保证了CO、CO2的较高转化率。另外,该反应器还解决了催化剂热点温度过高的问题。
针对焦炉煤气甲烷化反应深度问题,上海华西自主研发了的高活性、抗积碳、耐高温的焦炉煤气甲烷化专用催化剂。甲烷化工艺过程图见图2 所示:
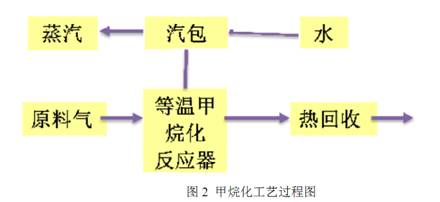
如图2所示,净化后的焦炉煤气,主要含有H2、CH4、CO、CO2、N2等,通过换热到300~350℃进入脱硫,以250~300℃进入甲烷化反应器,其中在甲烷化后气体中H2含量>5%,一氧化碳转化率≥99.95%,二氧化碳转化率≥≥999.9%,反应器出口CO、CO2<50ppm,同时副产蒸气。该流程有以下几个优点::
a. 工艺流程短、易于工程工程实施;
b. 工艺气一次通过甲甲烷化烷化反应器,无循环气、循环压缩机,实实现现投资投资最最小小
化、利润最大化;
c. 工艺设备少,只只有一有一台台甲烷化反应甲烷化反应器器和一台汽包。
d. 对原料气中的CO、COCO2 容忍度高、适应性强。
3.2 绝热多段固定定床床循循环环工艺工艺
该工艺工艺是是 一一段或二段段或二段甲烷化甲烷化后后的工艺气的工艺气循循环环至至一一段段甲烷化人甲烷化人口口,以““稀释”
进入一段甲烷化的CO+CO2 含含量量,示意图如图3 所示
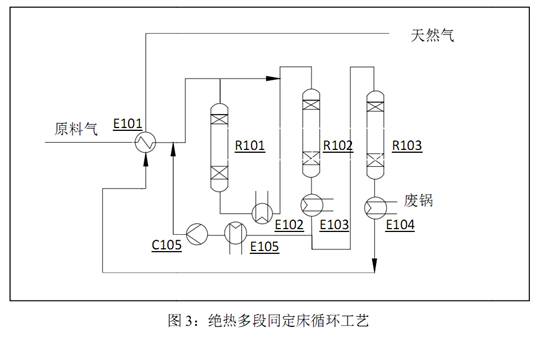
循环工艺可以调节循环量从而调节一段甲烷化运行温度,如可使甲烷化催化剂在450以下运行,从而降低了催化剂和反应器耐高温的技术要求。但是循环工艺中由于较大的循环比,能耗较高,且所需的循环压缩机增加了甲烷化工艺的总投资。
3.3 绝热多段固定床“一次通过”工艺
“一次通过”工艺是指无需工艺气段间循环,而是往一段甲烷化中混入一定量水蒸气,从而控制甲烷化反应的温升及结炭,示意图如图4 所示。

“一次通过”工艺较简单,能耗较低,可副产高品质蒸汽;无需循环压缩机,可大大节省投资。该工艺可使催化剂在500°C 以 运行,对催化剂和反应器要求较高;同时“一次通过”工艺需要补加较大量蒸汽(≥15%vol).增加了运行难度。
各种不同流程的甲烷化工艺比较见表1
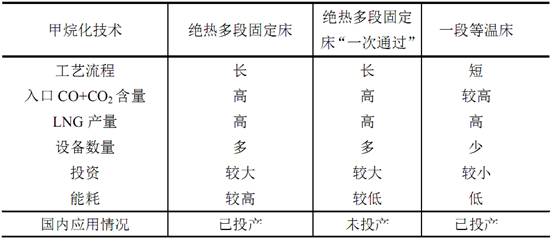
从表可以看出,一段等温床甲烷化技术与多段绝热甲烷化技术相比,具有工艺流程短、工艺简单、反应器数量少、投资省、能耗低的特点。据初步估算,上海华西公司开发的一段等温床甲烷化技术与国外多段甲烷化技术相比,该部分投资降低约70%以上。
4. 结语
焦炉煤气制天然气项目已成为焦炉煤气综合利用的热点技术之一,而甲烷化技术又是焦炉煤气制天然气项目、以及煤制天然气中的关键技术之一,迄今为止, 有长期运行的商业化应用实例较少。上海华西公司开发的等温甲烷化反应器工艺,流程短、能耗低、投资小,采用该工艺的LNG 工厂已顺利投产,为解决日后国
内焦炉煤气制LNG 提供了一条新工艺,也为焦炉煤气制LNG工业化取得了可贵数据和宝贵经验。